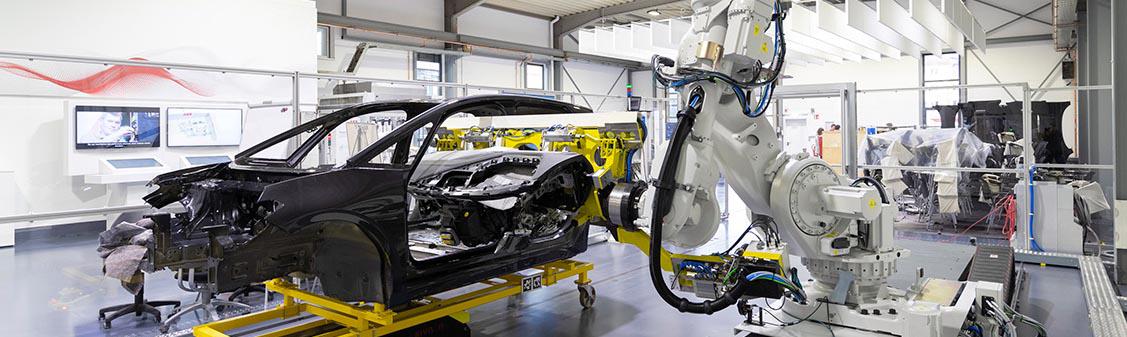
Project introduction
The project is the application of automatic transfer and stacking into boxes of trolley protective bottom plate after stamping and forming in GAC stamping plant.
Innovation point
The workpiece is transported at a moving speed of 750mm/S on the belt, and the workpiece is captured and positioned by the vision system and then grasped by the robot. The difficulty lies in follow-up grab.
Performance indicators
Size of grasping workpiece: 1700MM×1500MM; weight of workpiece: 20KG; material of workpiece: Q235A; working at full load can realize A transfer and packing capacity of 3600 pieces per hour is achieved at full capacity.
Typicality and representativeness
The project uses a visual system to dynamically capture and position the workpiece moving along the conveyor line, and draws the workpiece with the tooling and realizes the workpiece transportation through robot movement, and stacks the workpiece into boxes in situ. It can be widely used for material handling and logistics transportation in the production workshop of the same type of products in automobile factory. It can also be extended to the material handling and logistics transportation operations between latter processes after steel plate processing or injection molding.
Production line benefit
The automation line can save 12 workers, or 36 workers if the automobile factory runs on three shifts. Calculated at the labor cost of 70,000 per worker per year, annual savings amounted to 2.52 million Yuan, and the project can be paid back in the current year.
The automation line uses RB165 robot independently developed and manufactured, and the production rhythm is 6S/piece, which is at the same level as the operation rhythm of foreign brand robot.
This project has been successfully applied to GAC, breaking the monopoly of foreign brand robots in this field, and is at the leading level in China.
Customer reputation
1. It can realize uninterrupted operation and improve production efficiency;
2. Improve product quality and consistency;
3. Reduce the consumption of energy resource, and reduce environmental pollution during production process;
4. Save manpower and reduce risk of industrial injury;
5. The robot has stable performance, low failure rate of parts and simple maintenance requirements;
6. The production line has a compact structure and makes reasonable use of space.